Solar Thermal Collectors & Metal Coils
Thin layers of specialized coatings are applied to metal coils using techniques like magnetron sputtering to create a wide range of functional and aesthetic variations.
Thin-film coatings can be engineered to create highly reflective surfaces like mirrors and reflective coatings for solar, automotive, and architectural applications. Colored and decorative surfaces are designed by controlling the thickness and composition of the coatings. This allows for unique and customizable aesthetic variations.
Thin film coatings can be applied to metal coils to impart advanced functionalities, such as catalytic properties, corrosion protection, increased electrical conductivity, hydrophobicity, and oleophobicity.
Metal coil vacuum coating technology is an efficient method to apply a thin film coating onto metal coils with high throughput and uniformity. AGC's continuous air-to-air coil coating tool enables the production of high-quality, functional coatings on a range of metal substrates, including copper, aluminum, steel, and zinc-coated steel. Unlike traditional wet painting methods, the environmentally sustainable sputtering process eliminates waste, saves energy, and requires no hazardous chemicals . The continuous process offers flexibility for customized large area coating solutions for high-volume industrial applications, such as solar thermal collectors, reflectors, and bipolar plate coatings for electrolyzers and fuel cells.
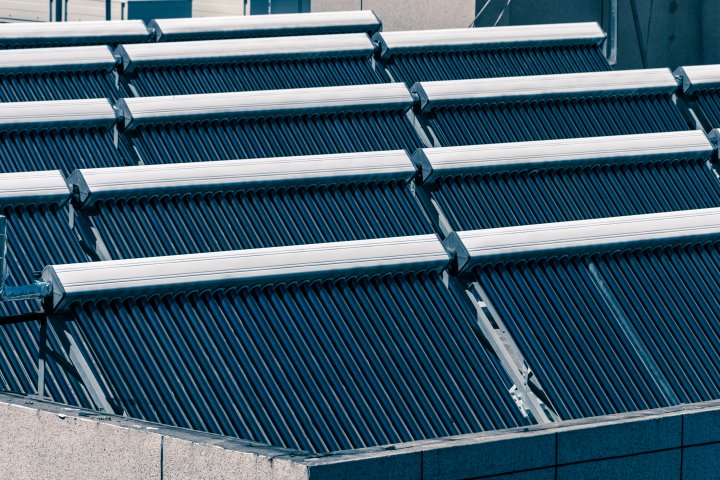
Solar thermal collectors use solar energy to heat a fluid or air, which is subsequently used to generate steam for electricity generation. High-efficiency thermal solar collectors often use spectrally-selective coatings to maximize the amount of solar energy they absorb, while minimizing the amount of heat they emit. Such coatings are typically made of metal or metal oxide films that are deposited onto the surface of the collector using techniques like magnetron sputtering. Aluminum and copper are both commonly used as substrates for these coatings because they are good conductors of heat and are relatively inexpensive. By applying a spectrally-selective coating to the surface of the metal, it is possible to achieve high solar absorptance (i.e., absorb more sunlight) while also reducing heat loss through thermal radiation (i.e., emit less heat). Solar absorptance of 95% and a thermal emissivity below 5% are typical performance targets for such coatings.
Reflectors are used in a wide variety of applications like lighting and horticulture. Such applications require high reflection for a well-defined range in the solar spectrum, while ensuring satisfactory coating integrity, durability, and U.V. resistance for a long lifetime of the reflector.
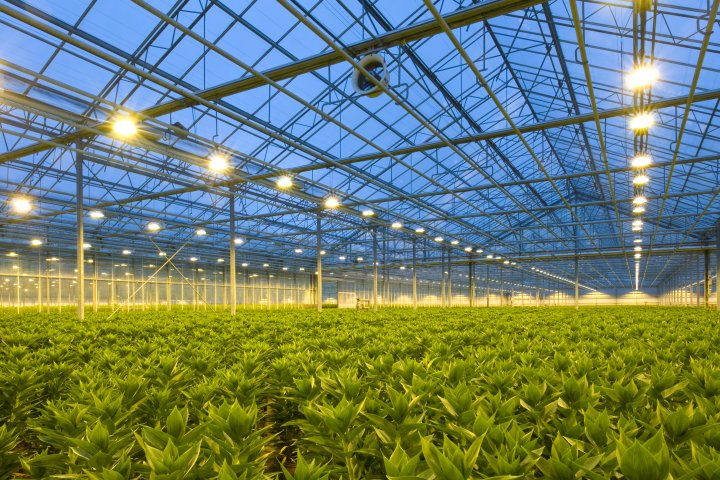
In electrolyzers, water is split into hydrogen and oxygen using an electrical current. The process involves passing the water through an electrolyte and applying an electric current across the electrodes, which causes the water molecules to break apart into hydrogen and oxygen. Fuel cells work in the opposite direction, combining hydrogen and oxygen to produce electricity and water. The process involves passing hydrogen gas over a catalyst and combining it with oxygen from the air to generate an electrical current.
In both electrolyzers and fuel cells, the components that come into contact with the electrolyte, gases, or catalysts are exposed to harsh environments that cause corrosion and degradation over time. Magnetron sputtering processes are used to address this issue by depositing protective coatings on these components, such as the bipolar plate.
Magnetron sputtering coatings provide a range of benefits, such as improved resistance to corrosion, wear, and chemical attack. Coatings are tailored to meet specific performance requirements, such as high conductivity, low friction, or high wear resistance, which improves overall efficiency and performance of the electrolyzers and fuel cells.
Features
- Enhanced performance and durability with protective layer for wear resistance
- Environmentally sustainable process does not use solvents or generate harmful emissions
- Cost-effective batch or continuous air-to-air process
- Customizable aesthetics from wide range of colors and finishes